5S Consulting
Sort, Set in order, Shine, Standardize, and Sustain are tools of lean process improvement that build visual factory and workplace organization. These tools can be applied in almost any situation; around a machine, in an office, shipping department, inventory room, and even in your own garage. The goal is improved productivity and ownership by the worker
Sort:
What don’t we need here? What do we need and how much of it do we need? Observe the work being done and incorporate knowledge from the workers help to analyze the situation and make good decisions on what truly belongs. Having unneeded things in the area like excess inventory, rarely used tools, fixtures or even information will negatively impact a worker’s ability to be effective.
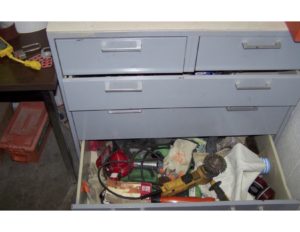
Set in order:
Now that we know what we want in the area, where should it go? Again the workers in the area guide the layout and flow improvement process. What steps are wasted that we can eliminate? How can we rearrange the furniture, supplies and tools to reduce the excess motion that the worker has to do? We review the inputs and outputs from the process and make sure the new layout supports optimum flow.
Shine:
Cleaning is obviously a component of this 3rd important step. It is critical that the area be maintained in a clean orderly fashion for better flow and productivity. But going a step further, we inspect through cleaning. What do we inspect? The machines, tools, and basically everything the worker depends upon to do the job. Are there areas of neglect like hoses, leaks, unreadable gages? When we shine we revisit the maintenance and condition of all these resources and make sure they perform as designed, and do so safely
Standardize:
Now that we have accomplished the first 3 elements of 5S we need to lock in the gains. We have eliminated the excess things, cleaned and improved the area and organized it for optimum flow. Now let’s make sure it stays that way. Step 4, Standardize, introduces controls that workers follow to keep organized. We use labeling and visual controls like signs and color coding to make it easier to know where things are, and where they go when we are finished using them. Techniques like Shadow Boards and other Point-of use-storage (POUS) further facilitate easier put-away systems so other workers can take advantage of quickly locating needed tools. Additional visual controls can also manage actual work and inventory flow as well as add visibility to performance and any problems that are occurring. The benefits of Visual Factory are that in real time we get immediate feedback of conditions that need attention.
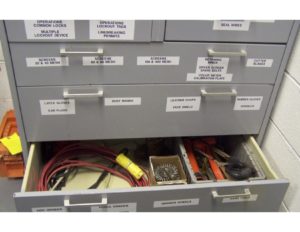
Sustain:
Arguably the most difficult step in the 5S process; continuing what you started. Having daily check and audits will force the process to work for us, not us work for it. 5S audits are a great way to see the continuous improvement because these audits are based on prior issues that have now been fixed. Training and discipline are needed as well as an open mind for improvement.
Please contact us for any of your lean 5S needs in the Philadelphia, PA region or across the country.