Case Study: Standard Work and Cellular Manufacturing
A small furniture manufacturing company purchased two new machines with the goal of doubling their output. After a period of time, however, they were not realizing the results of their investment and wanted to find out why. They hired Prosit to identify problems and come up with solutions to address them.
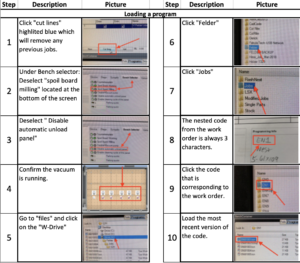
The first problem was that material carts were not being utilized correctly, specifically the necessary material required by the internal downstream customer was on the bottom of the cart. This forced the downstream customer to repeatedly take material off the cart to get to that material. The second problem was that only the owner and one other employee were trained to operate the machines. As a consequence, there was zero standard work for a very lengthy standard operating procedure (SOP).
Prosit’s consultant met the owner and managers to clearly define the specific goals for the engagement. This was a five-day contract over a period of three months. First, the consultant observed on the shop floor with the operator to see how the new machines worked. They went step-by-step, documenting and taking pictures of each step to better understand the process of both machines. In addition, two employees outside the normal scope of the machine operation observed, accomplishing a preliminary cross training. Finally, the consultant worked with internal downstream customers to achieve the ideal material presentation for them on the carts.
The information gathered for running the new machines was put into two separate standard work documents that were each one page long. The standard work simplified training for any other employees by summarizing the lengthy SOP into a 30-second lesson. Any employee can now use the standard work to get the machine warmed up, run specific programs, and properly turn the machine off.
The interviews with internal downstream customers were then used to go upstream and show the employees how their internal customer would need to have the material stacked. This resulted in employees being presented the material in a top down fashion with the ability to pull material directly from the top. The efficiency and productivity gains have made the customer quite pleased.
Please contact Prosit to see how we can help your company thrive too!