Case Study: The Value of Effective 5S Events
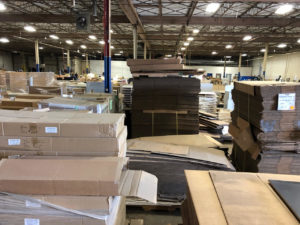
Piles of Material Moved During 5S Project
A high-end display company needed Prosit’s expertise to help them conduct a successful 5S event. This company does not have extra space due to the nature of their work. The material is large particle board which does not store easily, is heavy to move, and cannot be stacked because of possible scratching. This company needed an effective way to condense, store, and identify parts for each job running.
The 5S event was conducted over three days with a team of six employees, one from each department and two from the immediate area being optimized. The team created seven lanes for all work-in-process (WIP) and then an additional four lanes to be used as future work.
Since the work It can be further used as a temporary holding area for jobs that exceed the allotted lane, since the work this company does is mostly custom and rarely similar. The lanes were labeled with relocatable signs, creating a fluid staging area. The signs were also dry erase so when a new job arrived the old job number could be erased.
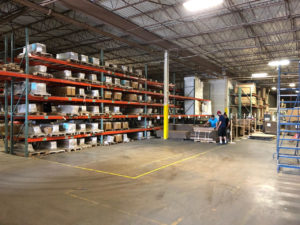
Final Optimized Area from 5S Project
The visuals created a more physical look at what work is being done on a daily basis. This resulted in the company’s ability to now schedule work properly for the assembly process. Also, the upstream office can visually see how much work is in line and can deliver more accurate dates to clients. The shop floor is more organized and job material is not getting mixed in with other jobs available.
The biggest improvement is sustainability – one employee each week, outside of the immediate environment, audits the area to ensure it is staying compliant with the new procedure. If it is not, the stakeholders in the process are notified and the team revisits the area and assesses what went wrong. This event has now generated additional kaizens with this client in different areas to discover other improvement opportunities.