Case Study: Visuals, Workplace Organization and Accountability
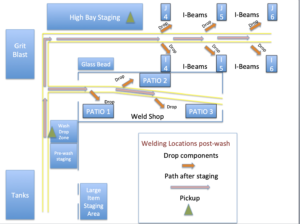
A client approached Prosit needing immediate assistance in helping a brand new management team establish basic visuals, implement workplace organization and enforce accountability within their operations.
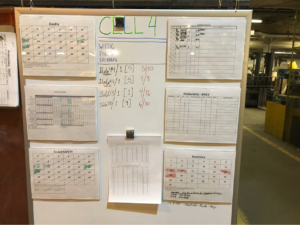
The operators were clocking in and out of jobs as they pleased which affected the accuracy of internal reporting including work content duration per job data. In addition, the new management team did not understand the value of continuous improvement. Consequently, setting up visuals and workplace organization was not initially on their radar.
Prosit has the unique ability to tackle the strategic and tactical side of these issues. Prosit first worked with the management team by conducting weekly meetings to track how well the new team was implementing the lean approach.
Secondly, Prosit led efforts on the shop floor to set up white boards, get input from operators on how they would want the process to work, work with supervisors to understand material flow, gather data for capacity models, and interview shop floor employees to identify the work flow. Prosit then rolled out a plan-to-actual program to assist in capturing real time work content for specific jobs.
Creating these systems has now given the new management team tools to effectively conduct workflow through the shop. The strategic training has initiated the management team to create 5S success boards for workplace organization. The plan-to-actual sheets are also assisting in the ability of supervisors to properly schedule and balance work throughout their respective departments.
Please contact Prosit to see how we can help your company too.